Automatic Edge Banding Machines Supplier in UAE
- A-one Machinery
- 1 day ago
- 7 min read
automatic edge banding machine supplier in UAE
2025 Top Automatic Edge Bander Machine with Trimmer
In today's woodworking, technology has changed how things are made. One important tool is the automatic edge banding machine. This machine helps woodworkers improve their skill and speed. This article will explain how these machines work and why they are important for modern woodworking.
The Evolution of Edge Banding in Woodworking
Edge banding, the practice of applying a narrow strip of material to the edges of wood panels, plays a crucial role in enhancing the aesthetic appeal and durability of wood products. Traditionally, this process was labor-intensive and time-consuming, relying heavily on manual dexterity and precision. However, with the advent of automatic edge banding machines, the woodworking industry has witnessed a paradigm shift.
Historical Context and Traditional Techniques
Edge banding has roots that trace back to ancient woodworking practices where craftsmen used rudimentary tools to apply decorative and protective edges to wood panels. Traditional methods required a high level of skill and patience, often involving manual cutting, gluing, and pressing of edge materials. The craftsmanship required for these tasks was significant, but the process was fraught with inconsistencies due to human error.
The Shift Toward Automation
The shift from manual to automated edge banding was driven by the need to improve efficiency and consistency. As technology evolved, the woodworking industry began to embrace machinery that could replicate the precision of human hands, but at a much faster pace. This transition allowed woodworkers to produce higher volumes of work without compromising on quality, setting the stage for modern automated systems.
The Role of Technological Advances
Technological advances in electronics and material sciences have been pivotal in the development of automatic edge banding machines. Innovations such as computer numerical control (CNC) systems and advanced sensor technologies have enabled machines to perform complex tasks with minimal human intervention. These technologies ensure precision and adaptability, allowing for seamless integration of edge bands across various materials and designs.
Understanding Automatic Edge Banding Machines
Automatic edge banding machines represent a synthesis of advanced engineering and cutting-edge technology. These machines automate the application of edge bands, ensuring uniformity and precision that surpasses manual methods. Equipped with sophisticated sensors and control systems, they can accommodate a wide array of materials, including PVC, ABS, wood veneer, and melamine, thereby offering versatility in design and application.
Core Components of Automatic Edge Banding Machines
The anatomy of an automatic edge banding machine consists of several key components that work in harmony to deliver flawless results. These include pre-milling units, gluing stations, edge application systems, end trimming units, and buffing stations. Each component is designed with precision to ensure the smooth operation and high-quality output of the machine.
Material Compatibility and Versatility
One of the standout features of automatic edge banding machines is their ability to handle a diverse range of materials. From PVC and ABS to more traditional options like wood veneer and melamine, these machines can adapt to various project requirements. This versatility not only broadens the scope of potential designs but also allows woodworkers to cater to a wider client base with varying preferences.
The Role of Sensors and Control Systems
The integration of sophisticated sensors and control systems is what sets modern edge banding machines apart from their predecessors. These technologies allow for real-time monitoring and adjustments, ensuring that each edge band is applied with precision. Sensors can detect inconsistencies or misalignments, enabling immediate corrections that enhance the overall quality of the final product.
The Mechanisms Behind Automatic Banding Equipment
Automatic edge banding machines operate through a series of meticulously engineered mechanisms. These machines typically consist of several integral components, including pre-milling units, gluing stations, edge application systems, end trimming units, and buffing stations. Each component plays a distinct role in ensuring the seamless application of edge bands.
Pre-Milling and Surface Preparation
The pre-milling unit is the initial stage where panel edges are prepared. This involves removing surface imperfections and creating a smooth substrate for adhesive application. This step is crucial as it ensures that the edges are clean and even, providing a perfect base for subsequent gluing. The precision of pre-milling directly impacts the effectiveness of the adhesive and the overall quality of the edge banding.
Advanced Adhesive Application Techniques
The gluing station is where a uniform layer of adhesive is applied to the panel edge. Using advanced application techniques, these machines ensure that the adhesive is evenly distributed, which is vital for optimal adhesion. The type of adhesive used can vary depending on the material of the edge band, and machines often allow for adjustments to cater to different adhesive types and viscosities.
Precision Edge Application and Trimming
Once the adhesive is applied, the edge band is aligned and pressed onto the panel edge through an edge application system. This system can accommodate varying thicknesses and widths, making it adaptable to diverse project requirements. After the edge band is applied, the end trimming unit executes precise cuts to remove any excess material, ensuring a neat and seamless integration.
Buffing and Finishing for Enhanced Aesthetics
The final stage of the process involves buffing and finishing. The machine polishes the edge band, enhancing its visual appeal and tactile quality. This stage not only improves the aesthetic refinement of the product but also adds a protective layer that extends its durability. The buffing process is crucial for achieving a polished look that meets high-quality standards.
Advantages of Automatic Edge Banding Machines
The deployment of automatic edge banding machines confers a multitude of advantages, transcending traditional manual methods. These advantages encompass enhanced efficiency, improved precision, and elevated quality in woodworking endeavors.
Boosting Production Efficiency and Throughput
Automatic edge banding machines significantly expedite the edge banding process, reducing production time and labor costs. By automating repetitive tasks, these machines allow skilled craftsmen to focus on more intricate aspects of woodworking. This optimization of resource allocation maximizes throughput, enabling businesses to meet increasing demand without compromising on quality.
Achieving Unmatched Precision and Consistency
The precision afforded by automatic banding equipment is unparalleled. These machines ensure consistent application of edge bands, eliminating human errors and variations inherent in manual processes. The result is a final product that exhibits a level of uniformity and quality that enhances its marketability and consumer appeal.
Expanding Creative Possibilities with Versatility
Automatic edge banding machines are designed to accommodate a wide spectrum of materials and dimensions, offering versatility in design and application. This adaptability enables woodworkers to cater to diverse client preferences and project specifications. The ability to work with different materials fosters creativity and innovation, allowing for the exploration of new design possibilities.
Enhancing Quality and Reducing Waste
The precision and efficiency of automatic edge banding machines contribute to superior product quality while minimizing material wastage. The reduction in errors and rework not only enhances the economic viability of woodworking operations but also aligns with sustainable practices by minimizing resource consumption. This focus on quality and sustainability appeals to environmentally conscious consumers.
Integrating Automatic Edge Banding Machines into Your Workflow
The integration of automatic edge banding machines into a woodworking workflow necessitates careful planning and consideration. Factors such as workspace configuration, machine compatibility, and operator training are pivotal in ensuring a seamless transition and optimal utilization of the equipment.
Evaluating Workspace Requirements and Infrastructure
Prior to acquiring automatic banding equipment, it is imperative to assess the existing workspace and infrastructure. Adequate space must be allocated to accommodate the machine and its operational requirements, including power supply and ventilation. A well-organized workflow facilitates efficient material handling and minimizes bottlenecks, ensuring smooth operations.
Selecting the Right Machine for Your Needs
Choosing an automatic edge banding machine that aligns with the specific needs and objectives of your woodworking operations is crucial. Considerations such as the types of materials used, production volume, and desired features should guide the selection process. Customization options may also be explored to tailor the machine to unique project demands, maximizing its functionality and efficiency.
Training Operators for Optimal Performance
The successful deployment of automatic edge banding machines hinges on the proficiency of the operators. Comprehensive training programs should be implemented to familiarize operators with the machine's functionalities, safety protocols, and maintenance requirements. Continuous skill development initiatives can further enhance operator competence and contribute to sustained operational excellence.
Company Information
automatic edge banding machine supplier in UAE
For more information about our products and services, please contact us:
Kaneez A One Machinery Trading LLC Phone: 0565371007
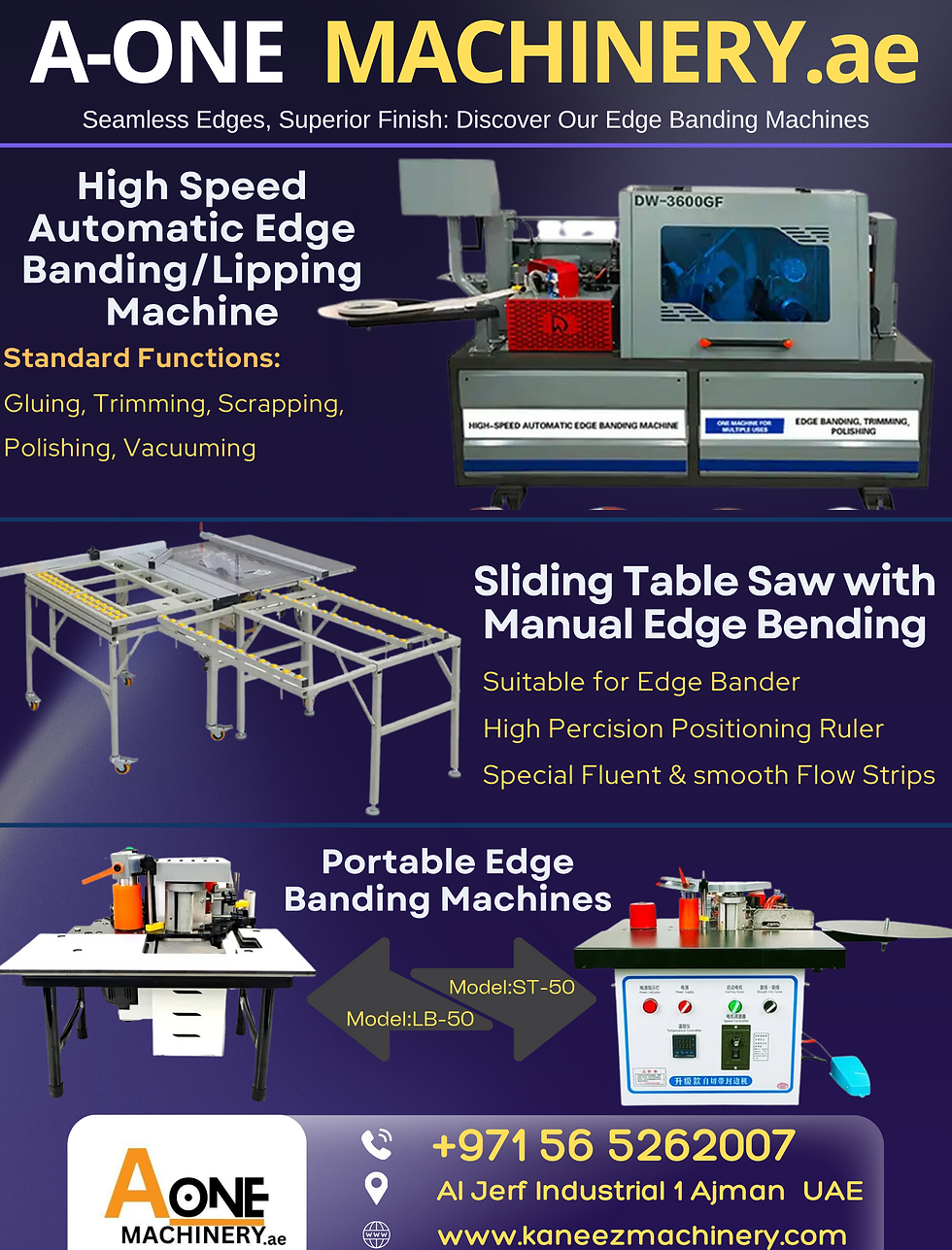
The Future of Woodworking with Automatic Edge Banding Machines
The trajectory of woodworking is inextricably linked to advancements in automation and technology. As automatic edge banding machines continue to evolve, they are poised to redefine the boundaries of craftsmanship and efficiency in woodworking. The integration of artificial intelligence, machine learning, and IoT capabilities holds the potential to further enhance the capabilities of these machines, ushering in a new era of innovation and excellence.
Advancements in Automation and Technology
The future of woodworking is bright with the continuous advancements in automation and technology. Future iterations of automatic edge banding machines will likely incorporate more sophisticated AI and machine learning algorithms. These advancements will enable machines to learn and adapt to different materials and processes, further enhancing precision and efficiency.
Embracing Artificial Intelligence and Machine Learning
The integration of artificial intelligence and machine learning into edge banding machines could revolutionize the industry. These technologies can facilitate predictive maintenance, reducing downtime and extending the lifespan of machines. Additionally, AI can help in optimizing production processes, ensuring that the machines operate at peak efficiency at all times.
The Role of IoT in Enhancing Connectivity and Efficiency
The Internet of Things (IoT) is set to play a significant role in the future of automatic edge banding machines. IoT connectivity allows machines to communicate with other devices and systems, enabling real-time monitoring and data analysis. This connectivity can lead to more efficient production processes and rapid identification and resolution of potential issues.
In conclusion, automatic edge banding machines represent a pivotal advancement in the woodworking industry, offering a myriad of benefits that extend beyond traditional methods. Their ability to enhance efficiency, precision, and quality positions them as indispensable tools in the pursuit of excellence in woodworking. As the industry continues to embrace automation, the role of these machines will undoubtedly expand, shaping the future of woodworking for generations to come.
If you need any further modifications or additions, feel free to ask!
Comments